By: Casey Bennett, Director of Fire Technologies
As a technology leader in the fire space, one reality we must remain aware of is that the systems we provide at Tech Electronics are only of value if they’re in good working order. That’s where inspections come in.
Business owners and facility managers generally do not look forward to their code-required system inspections, and I understand why. Inspections cost money and time, and can be disruptive to the day-to-day operations of a business. However, they are a crucial part of ensuring your life safety technology is up to scratch, and must be completed with proper procedures.
Tech maintains a very high standard when it comes to our inspections, and one of the people responsible for enforcing that standard is our new Inspector Operations Manager, Lorenzo Smith. I invited Lorenzo for a quick chat about life safety, his new role, and how he intends to continue to drive Tech’s pursuit of excellence in the space.
Casey: As I’ve told you already, it’s great to have you on board.
Lorenzo: It’s great to be on board! Getting up to speed is always a process, obviously, but it’s incredibly motivating to have joined a great team and being able to look ahead to the big things we can accomplish together.
Detection Inspection
Casey: Let’s talk about standards, because frankly, a disturbing trend everyone is aware of in industry circles is inspectors taking shortcuts rather than conducting proper inspections. For instance, with smoke detectors, the NFPA very clearly outlines what is required for a functional inspection – there must be actual smoke entry into the detection chamber for a proper test to occur.
Instead, you often hear about inspectors using magnets, which simulate the alarm condition electronically, but don’t functionally test the device’s detection chamber. That’s a huge problem. Imagine if there was a fire, but it turns out that the nearest detector, while capable of setting off an alarm via proper electrical connection to the panel, wasn’t properly detecting the smoke to do so. That puts lives in danger.
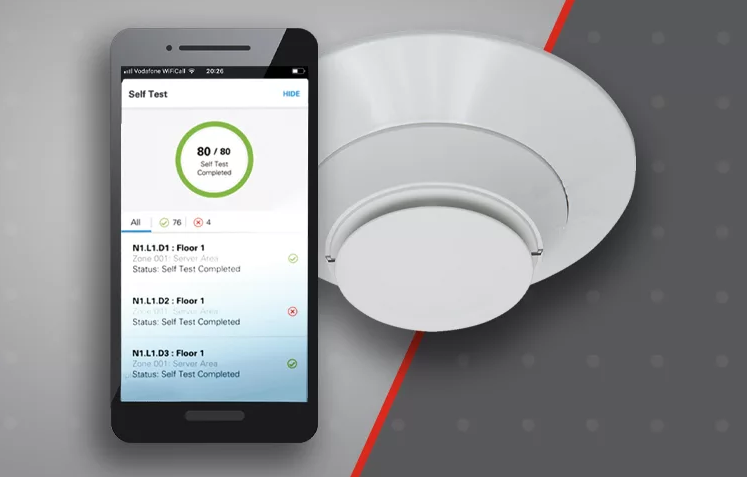
Lorenzo: Agreed. While it’s totally unacceptable, I think it’s important to understand why that’s happening. In many cases, I doubt that these inspectors are setting out to cut corners, but that kind of thing can happen when everybody is rushing to get things done as quickly as possible to keep costs down. In my opinion, standards don’t usually fall off overnight; they erode over time when one compromise leads to another.
In a lot of cases, the first compromise starts with cost-cutting to compete on price. We know price does matter to customers. Apart from enforcing high standards, Tech is also fortunate to have technologies like Notifier’s self-testing detectors, which make functional tests on detectors much quicker, less intrusive, and more efficient. That optimization introduces cost-savings without compromising safety.
Setting A Culture
Casey: What about in instances where there isn’t a convenient time-saving technology to make things simpler for everyone? For example, I often hear about inspectors skipping the step of functionally testing a pull station, and instead just opening the device with a key or screwdriver to simulate the activation. I’ve seen many firsthand examples of why that’s a problem, where a broken piece of the device was occluding the pull-down mechanism, and an inspector taking shortcuts wouldn’t have caught it due to not functionally activating that mechanism during their test.
Lorenzo: Yeah, I’m sure it does happen. The antidote to that, in my opinion, is culture, and one thing that’s clear to me is that I’m taking on this role in an organization where a culture of “doing it right” is already the norm. In my experience, that kind of culture isn’t built overnight – just like doing a proper inspection, there are no shortcuts.
It requires finding talented and motivated people, developing them through training and education, and continuing the process every day in the field. Standardization is key. We must foster an environment in which we do the same thing the same way – the right way – every time, and back that up with accountability. Tech is already a well-oiled machine in this way, so my job is about continuing to uphold those standards, as well as finding ways to fine tune our processes and make us more efficient, while never sacrificing quality.
What sets us apart?
Casey: As a former operations guy myself, I’m so glad to hear you say that. There’s so much that goes into a sound inspection process behind the scenes, a lot of which customers can’t see ahead of time. So what should they be looking for in an inspections provider?
Lorenzo: I would just start by asking some basic questions. Can the company speak to their inspectors’ qualifications? At Tech, our inspectors are required to obtain NICET certifications to progress through the ranks and demonstrate their competency. Are their inspectors able to conduct repairs on-site if they discover an issue? Our inspectors are trained and equipped for same-day repairs. How many inspectors do they have on staff? At Tech, we make a priority out of maintaining a sizable roster to maintain flexibility and responsiveness, and make sure we’re always meeting our customers’ needs.
Well Lorenzo, it was a pleasure chatting with you today and getting to hear your thoughts on all things inspections. If you’re looking for a provider to partner with for all your inspections needs, contact Tech today!