Regular fire alarm inspections are crucial in making sure your building is adequately protected in an emergency, but it’s no secret that most people aren’t looking forward to them. Inspections are often seen as time-consuming and disruptive, which is exactly what makes the innovation of self-testing detectors such an important step forward for the fire and life safety industry.
But how are they revolutionizing inspections? Let’s take a look at the mechanics of this exciting technology.
What makes traditional inspections a pain?
Traditionally, inspecting smoke detectors requires two technicians each filling a different role: one walking around conducting the inspections, and the other remaining at the panel viewing the results and – because the panel is in test mode – making sure that no other detector is going into alarm mode due to a real emergency.
The technician away from the panel must manually spray canned smoke into each detector, a process that can ultimately take several minutes per room. This process can also be significantly disrupted by issues like locked doors, occupied rooms, hard-to-reach areas like elevator shafts, and tall ceilings. Once these inspections have been completed, they must be transcribed, which takes additional time.
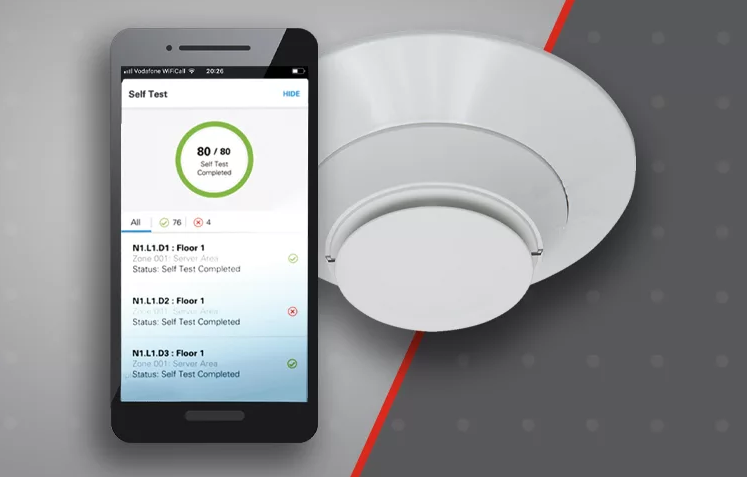
How do self-testing detectors work?
With Notifier’s Self-Test series of detectors, each unit can independently generate small amounts of smoke. This smoke is then introduced into the detection chamber, testing whether it is operating at full capacity. An anti-masking technology check also ensures that the smoke entry points are open, and allowing technicians to quickly identify if a detector’s smoke entry points have been blocked. The Self-Test detectors also each independently communicate with the technician’s mobile device via the mobile application, allowing them to verify the visual inspection.
What makes self-testing detectors so much more efficient?
To start, only one technician is necessary. The technician can initiate the self-testing function for all detectors in the building while at the panel, and can then make their way around the building to conduct quick visual inspections. Putting the alarm system into “test” mode for the entire inspection process is no longer necessary, so the system remains fully operational. Once inspections are completed, the report is automatically generated electronically via the Connected Life Safety Services (CLSS) platform, saving time and providing a clear audit trail for compliance purposes.
The Bottom Line
Depending on the size of the facility or campus, a traditional inspections process can take multiple days. With self-testing detectors, this could be cut down to mere hours. That means fewer disruptions over less time, and a lower overall cost. For large buildings, facilities and campuses, that’s a no brainer.